As the global economy becomes increasingly interconnected, supply chain risk management has evolved into an essential pillar for companies looking to stay competitive and resilient. Businesses must navigate a complex web of supplier relationships, and as a result, the need for holistic, technology-driven solutions that increase supply chain visibility has grown immensely.
In fact, 70% of organizations are now prioritizing supply chain visibility and resilience as key areas for technological investment. This shift is driven by a recognition that, with the right tools, companies can not only monitor their suppliers more effectively but also ensure regulatory compliance, reduce risks, and improve overall performance across every link of the supply chain.
This guide explores how enterprise technology can transform supply chain risk management from a fragmented, reactive process into a comprehensive, proactive strategy.
What Is Supply Chain Risk Management?
Supply chain disruptions impact more than profits; they can damage brand reputation, lower customer satisfaction, create compliance issues, and hinder corporate responsibility efforts. Yet today’s global supply chains remain vulnerable, and common strategies like just-in-time inventory can worsen shocks.
Many organizations lack the ability to assess risk and work with suppliers to mitigate it effectively. Protecting supply chains without risky trade-offs requires a fundamental rethink.
Supply Chain Risk Management (SCRM) is the first critical step, focusing on identifying, assessing, and reducing risks across the supply chain. This includes monitoring suppliers, logistics, and distribution channels to prevent disruptions, compliance breaches, and reputational risks.
SCRM’s goal is to ensure timely, cost-effective delivery without compromising quality or customer satisfaction. In complex, global supply chains, SCRM is essential for managing risks from natural disasters, political instability, or cyberattacks. Effective SCRM prepares companies for these risks, with contingency plans like backup suppliers for example.
Why Is a Supply Chain Risk Management Plan Important?
Supply chain risk management is essential to maintaining business continuity and safeguarding an organization’s operations, profitability, and reputation. A single breakdown in the supply chain can hinder a company’s ability to deliver products and services, potentially eroding customer trust and loyalty. For this reason, businesses must take a proactive approach to identify, assess, and mitigate risks before they become problems.
Building operational resilience in supply chains through proactive planning and risk management is crucial. Companies that invest in robust risk management processes are better equipped to withstand unforeseen challenges and recover more quickly when disruptions occur. According to KPMG, “Risk management is no longer a back-office function – it’s now central to business strategy, with more than 70% of companies prioritizing risk resilience as a top investment.”
Types of Supply Chain Risks
Let’s take a closer look at some of the most pressing supply chain risks:
Internal Risks
Internal risks stem from within the organization or its immediate operations. These can often be managed with a high degree of control but, if left unchecked, can cause severe disruptions.
- Business Risks/Operational Risks: Inefficiencies or poor management practices can lead to bottlenecks, quality control issues, and missed deadlines.
- Financial Risks: Cost volatility, fluctuating demand, and cash flow issues create financial uncertainty, which can lead to compromised supplier relationships or cutbacks in inventory.
- Manufacturing Risks: Delays in production, equipment malfunctions, and labor shortages can have a domino effect on product availability.
- Contract and Compliance Risks: Managing service-level agreements (SLAs) and upholding contract terms is vital to minimizing legal exposure. Non-compliance with terms such as right-to-audit clauses or regulatory requirements can lead to penalties, strained relationships, and costly legal challenges.
External Risks
External risks arise from factors outside the organization’s direct control, such as third-party suppliers, geopolitical factors, or environmental changes. These risks require vigilant monitoring and adaptive strategies to mitigate anything potentially disrupting operations.
- Reputational Risks: A supplier’s misconduct or failure to meet standards can significantly damage a brand’s reputation.
- Cybersecurity Risks: With an increase in ransomware and IT disruptions, cybersecurity risks are an escalating concern. The Colonial Pipeline incident, which led to significant fuel shortages in 2021, serves as a stark reminder of how vulnerable supply chains are to cyber threats.
- Geopolitical Risks: Tariffs, government instability, and trade wars can disrupt sourcing and increase costs. For example, the U.S.-China trade war resulted in added tariffs on $380 billion worth of Chinese goods, creating supply chain challenges and financial strain for companies reliant on those imports.
- Environmental Risks: Climate change, natural disasters, and environmental regulations pose significant risks to supply chain continuity. In 2022 alone, the National Oceanic and Atmospheric Administration (NOAA) reported 18 separate billion-dollar climate and weather disasters in the United States, which led to widespread supply chain interruptions. Additionally, with the rise of ESG compliance requirements, companies are increasingly responsible for meeting environmental standards.
Challenges of Risk Management in the Supply Chain
Supply Chain Risks range from a lack of visibility and collaboration, to resistance, non-compliance and more. Let’s take a look at some of the biggest challenges in detail.
Complexity and Lack of Visibility
According to McKinsey, nearly 80% of supply chain executives have identified the need to improve visibility by investing in digital planning tools. A lack of insight into suppliers’ processes can lead to unanticipated disruptions and inefficiencies.
To address this, companies should implement integrated technology platforms, such as ERP systems, which allow for real-time data sharing and communication across the supply chain. These systems increase transparency and help detect potential issues early.
Inadequate Risk Assessment Frameworks
Many organizations lack a comprehensive risk assessment framework, which is detrimental to effective Supply Chain Risk Management (SCRM). Without such a framework, you may miss key threats, leading to vulnerabilities within the supply chain.
The solution is to develop a robust risk assessment framework that incorporates both qualitative and quantitative metrics. This framework should be adaptable, and regularly updated to respond to emerging threats and changes.
Resistance to Change within Organizations
Introducing new risk management practices can be challenging when there’s internal resistance to change, and buy-in is lacking across departments.
To avoid such resistance, be sure to foster a culture of risk awareness by training employees at all levels on the importance of SCRM. Engage leadership to promote risk management as a strategic priority, and encourage collaboration among cross-functional teams. Leadership advocacy and team involvement can help embed SCRM into the company culture, making it easier to adopt new practices.
As Deloitte points out, “Supply chain disruptions will continue to impact global markets, but companies that embrace predictive risk analytics and diversify their supplier base will have a strategic advantage.”
Supplier Non-Compliance and Performance Issues
Supplier non-compliance with agreed-upon standards and service-level agreements (SLAs) can lead to costly disruptions and reputational risks. Be sure to establish clear SLAs and compliance protocols with suppliers and perform regular audits to ensure these standards are met.
Technology platforms that continuously monitor supplier performance can provide real-time insights, allowing organizations to address non-compliance issues swiftly and hold suppliers accountable to agreed standards.
Environmental and Regulatory Changes
Environmental factors and regulatory requirements are constantly evolving, leading to increased risk and complexity. Climate events, new environmental standards, and regulatory demands can disrupt supply chains and increase compliance risks.
To proactively mitigate these types of risk, stay updated on regulatory requirements and industry standards, such as those set forth by the National Institute of Standards and Technology (NIST), by subscribing to relevant alerts and participating in industry forums. Additionally, incorporate environmental and regulatory factors into the risk assessment framework.
Cybersecurity Threats
From ransomware to phishing attacks, cybersecurity vulnerabilities can disrupt supply chain operations and compromise sensitive data. Be sure to invest in robust supply chain security measures and conduct regular security audits to identify and address vulnerabilities.
Employee training on cybersecurity best practices is also essential, as many security breaches result from human error. By educating employees and implementing stringent cybersecurity protocols, you can significantly reduce your exposure to cyber risks.
Procurement Strategy and Risk Management
For procurement to manage risk effectively, it must align closely with the organization’s risk management framework, setting goals that ensure the selection of reliable suppliers and identification of vulnerabilities throughout the supply chain. This strategy allows procurement teams to assess suppliers on risk factors like financial stability, compliance, resilience and scalability.
Challenges in procurement risk management include unpredictable market conditions, price fluctuations of raw materials, regulatory shifts, and supplier performance variability. A data-driven approach using historical data, real time insights, and predictive analytics can help procurement teams make informed decisions and anticipate disruptions.
For example, monitoring real-time supplier performance data reveals trends that may indicate future delays, enabling proactive action.
Market intelligence is also crucial, allowing teams to stay updated on supply-demand trends, geopolitical changes, and regulatory shifts, so they can forecast risks and adjust sourcing strategies.
Watch our webinar, Proactive Risk Management in a Changing Landscape, to hear four procurement experts tackle the challenges of risk management and examine proactive strategies for building supply chain resilience. You’ll learn how AI, risk mapping, and cross-functional collaboration can enhance supplier compliance and strengthen global supply chains against disruptions.
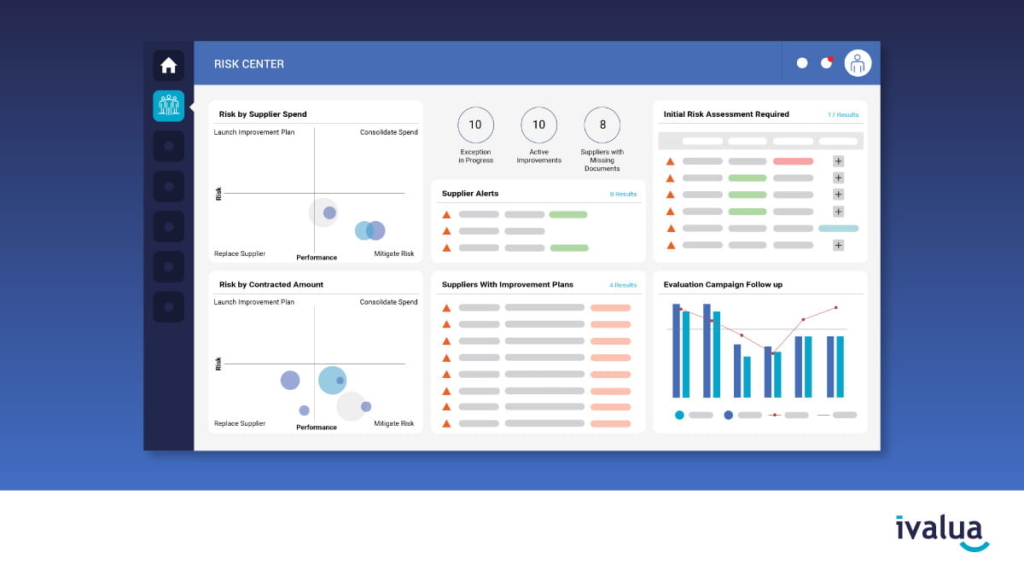
5 Key Steps for Effective Supply Chain Risk Management
Creating a robust supply chain risk mitigation framework is essential for identifying, assessing, and addressing risks that could disrupt your business operations. Here are 5 key steps.
1) Identify Risk:
This first step is critical to developing your risk mitigation framework and involves several sub-steps:
- SWOT Analysis: A SWOT analysis identifies internal strengths and weaknesses, as well as external opportunities and threats, offering a foundational perspective on potential risks.
- Failure Mode and Effects Analysis (FMEA): FMEA helps organizations prioritize risks by identifying specific failure points, estimating their impact, and determining mitigation priorities.
- ISO 31000: ISO 31000 provides guidelines on risk management best practices, offering a standardized approach to identifying, analyzing, and addressing risks. Effective risk identification hinges on two key factors: involving the right personnel – from operational staff to risk management specialists – and gathering essential documentation, such as compliance reports, supplier contracts, and process manuals, to enable a thorough supply chain risk analysis.
2) Assess Risk:
Once risks are identified organizations need to prioritize which risks to address first. A thorough risk assessment process evaluates how likely each risk is to occur and the potential consequences if it does. Consider the following:
- Likelihood and Impact: Assess each risk’s probability of occurrence and the severity of its impact on supply chain operations.
- Supplier Risk: Given that suppliers play a central role in supply chain stability, assessing supplier-related risks is critical. Evaluate suppliers based on financial stability, operational capacity, and compliance with regulations. Consider using supplier performance scorecards to track key metrics such as on-time delivery, quality standards, and incident rates.You should also try to assess their potential resilience. Do they have risk mitigation strategies in place?
- Third-Party Assurance: Verify third-party certifications, compliance, and quality standards to ensure suppliers meet necessary risk management requirements.
3) Integrate Risk Management into Your Overall Supply Chain Strategy:
Integrating risk management into your strategy aligns supply chain planning and decisions with risk priorities, enabling faster, more effective responses to disruptions. Involving cross-functional stakeholders – procurement, logistics, finance, compliance, and IT – ensures that all risks are considered and fosters a culture of risk awareness and accountability across departments.
4) Mitigate Risk:
Risk mitigation strategies are essential for reducing or eliminating identified risks and ensuring supply chain resilience. These strategies should be tailored to each risk type and its assessed impact:
- Diversification: Avoid dependence on any single source. As noted in “Global Supply Chains in a Post-Pandemic World” by Willy C. Shih in the Harvard Business Review, geopolitical risks, such as trade restrictions and national security issues, are prompting companies to rethink their reliance on single suppliers. To manage these risks, more companies are turning to multi-sourcing and diversifying their supply chains. This transition from “just-in-time” to “just-in-case” highlights the growing emphasis on building supply chain resilience to withstand disruptions from events like pandemics or geopolitical conflicts.
- Redundancy: Build redundancy into the supply chain, such as maintaining safety stock or securing secondary transportation routes, to mitigate potential disruptions.
- Strategic Partnerships: Develop relationships with key suppliers and logistics partners to improve communication and collaboration, facilitating faster response times to disruptions. Gartner highlights that in the evolving supply chain landscape, supplier collaboration has surged in priority, with 88% of procurement leaders emphasizing this aspect in the past two years. This trend suggests that better collaboration with suppliers is a critical tool for mitigating risks and maintaining continuity.
5) Monitoring and Review:
Ongoing oversight enables organizations to identify emerging risks and adjust mitigation strategies as needed. Implement real-time data tracking for supply chain performance and risk indicators. Integrated platforms like ERP systems can provide continuous insights into supplier performance, logistics status, and market conditions. Be sure to conduct regular reviews of risk management practices, updating the framework to reflect new risks or changes in the supply chain landscape.
Learn more about risk mitigation strategies in our blog, “Supplier Risk Assessments: Evaluate & Manage Vendor Risks.”
Strategies for Managing Supply Chain Risk
Effectively assessing risk and building supply chains with lower exposure will reduce the frequency and severity of disruptions, but not eliminate them. To mitigate the impact when they occur, companies must also adopt more sophisticated methodologies to model the effects of specific events.
An innovative approach is the stress tests developed by MIT professor David Simchi-Levi which revolve around two measures:
- Time to recover (TTR) is the amount of time a particular supply chain node needs to regain full capacity after a specific shock.
- Time to survive (TTS) is the maximum duration that the supply chain can match supply with demand after a facility disruption.
Calculating these for a range of possible scenarios helps to assess the financial impact of disruptions and devise appropriate contingency plans and inventory strategies.
The same applies to supply chains. A common response to recent supply shocks has been to begin shifting supply from China to local markets. That won’t necessarily reduce risk, just change the type of risk and increase costs.
For example, UK factories were forced to shut down in March during the pandemic, while Honda factories in Wuhan were reopening. A China + 1 strategy, now being considered by many organizations, would have ensured greater resilience at all stages of the pandemic while also mitigating the cost impact – as long as the +1 supplier has a distinct risk profile from the Chinese supplier, including sub-tier suppliers not exposed to China.
Successfully implementing such a portfolio approach requires the right talent and technology. Procurement and supply chain teams need to continue building the analytical skills of their teams. Technology can empower these teams by providing relevant data from internal, third-party and supplier sources to help derive actionable insights.
Establish Nearshore Sources (Friendshoring)
Nearshoring, or “friendshoring,” involves sourcing from nearby or allied countries to reduce supply chain risk and enhance stability. This approach decreases dependence on distant or unstable regions, shortens transit times, and improves responsiveness to market shifts, boosting resilience. It also strengthens trade relationships with reliable partners, adding predictability in an unpredictable global landscape.
Inventory Buffer and Safety Stock Management
A robust safety stock and inventory buffer are crucial for supply chain resilience, protecting against demand spikes and disruptions to ensure customer needs are met. An agile supply chain with effective buffer stock management prevents stockouts and lost revenue, enabling companies to adapt to sudden market changes.
Improve Supplier Visibility
As supply chains become more complex, understanding the interconnected web of suppliers across various tiers becomes vital. Improving visibility across all tiers allows businesses to anticipate potential risks, enhance transparency, and make informed decisions on managing supplier relationships and dependencies.
Model Worst-Case Scenarios
Building supply chain resilience involves modeling worst-case scenarios to uncover vulnerabilities and prepare strategic responses. Detailed business continuity plans (BCPs) enable companies to handle disruptions like supplier insolvency or natural disasters, ensuring continuity under challenging conditions and better crisis management.
Technological Tools for Real-Time Monitoring
Using advanced technologies like AI, procurement analytics, and predictive demand models is essential for real-time monitoring and proactive decision-making. AI insights enable businesses to anticipate disruptions, while predictive models help adjust strategies and align inventory levels. Regularly using these tools allows companies to quickly respond to market shifts and maintain continuous supply chain oversight.
Regular Supply Chain Risk Assessments
Frequent supply chain risk assessments are crucial for anticipating disruptions and maintaining resilience. Regular supplier risk evaluations help identify new risks, adapt to market shifts, and test the strength of mitigation strategies, ensuring long-term stability and continuity in an unpredictable market.
Internal Risk Awareness Training
Internal risk awareness training is essential for effective risk management. Educating employees about risks and their roles in mitigating them reduces supply chain vulnerabilities. Training should cover financial, compliance, cybersecurity, and operational risks, enabling teams to recognize early warning signs and follow best practices. Regular sessions reinforce risk management as a priority, ensuring teams are prepared to respond swiftly during crises.
Here’s a useful SRPM checklist to get your started with these strategies.
CACI Case Study
CACI, a leading provider of information solutions and services for national security and government transformation, faced significant challenges in its procurement and supply chain operations. The organization grappled with inefficiencies due to paper-based processes, limited visibility into supplier performance, and difficulties in ensuring compliance across its extensive supplier network.
CACI implemented Ivalua’s comprehensive Source-to-Pay (S2P) platform, which enabled them to digitize its procurement and accounts payable processes, achieving near-total paperless operations. The platform’s user-friendly interface and supplier-friendly model facilitated rapid adoption and streamlined supplier collaboration. Additionally, Ivalua’s flexibility allowed CACI to customize workflows and integrate best practices, enhancing overall efficiency.
CACI achieved 95% spend under management and 95% compliance in Procure-to-Pay (P2P) processes, leading to a 30% reduction in operating costs and a 30% increase in identified savings. Read the full CACI case study.
How Ivalua Can Help
Ivalua’s supply chain risk management software gives you the insights, tools, and flexibility you need to proactively manage supply chain risks. By centralizing data on supplier performance, compliance, and risk factors, it enhances visibility across all levels of the supply chain, so you can identify and mitigate potential issues before they escalate.
With capabilities for real-time monitoring, supplier assessments, and customizable dashboards, Ivalua you companies to strengthen supplier relationships, ensure compliance, and reduce disruptions.
Key features of Ivalua’s platform include
- Real-time risk monitoring, predictive analytics
- Third-party integration
- A user-friendly interface for seamless collaboration across departments
- Tools for supplier diversification and compliance management
- Robust data security
Learn how our supply chain collaboration software is designed to provide mission-critical agility and risk mitigation.
Modernizing Supply Chains for Resilience and Advantage
Supply chains are increasingly central to a company’s success or failure, offering a significant competitive edge when managed well. Effective risk management not only improves financial results but also reduces ethics breaches and supports sustainability goals. However, traditional methods are no longer sufficient for the demands of today’s global markets, requiring a comprehensive reevaluation of how risks are assessed, mitigated, and modeled.
While there’s no one-size-fits-all solution, certain best practices in talent, processes, and technology can drive better outcomes. Prudent leaders will implement these changes proactively to stay ahead. Continuous learning and adaptation are key to managing evolving risks, helping organizations remain resilient and responsive.
Start by watching our supply chain collaboration demo.