Supply chain collaboration is the cornerstone of modern business operations, facilitating seamless coordination and communication among various stakeholders involved in the production, distribution and delivery of goods and services. Collaboration is indispensable in modern business landscapes due to its critical role in driving innovation, enhancing agility, boosting employee engagement, and improving problem-solving.
However, the absence of effective collaboration significantly impacts an organization’s productivity. According to a 2023 survey, 52% of engineers spend at least six hours per week on supply chain-related work, including sourcing vendors, providing and requesting quotes, and ordering parts – a staggering 73% increase from 2022 to 2023. In contrast, when excellent supply chain collaboration strategies are in place, 63% of manufacturers surveyed report on-time delivery of more than 95%.
In essence, mastering the art of supply chain collaboration is not an option but a necessity for businesses aiming to stay at the forefront of their industries. Join us as we explore the transformative impact of collaborative practices on supply chain efficiency, resilience, and competitiveness, and how you can implement these strategies to propel your business to new heights.
What Is Supply Chain Collaboration?
Supply chain collaboration is a synchronized effort among internal departments and external partners across the supply chain network to achieve common goals and objectives. At its core, it entails an open exchange of information, joint allocation of resources, and shared responsibilities.
The objective is to streamline processes, boost operational efficiency, and substantially elevate the level of value delivered to customers. This synergetic effort not only enhances overall performance but also fosters resilience and agility within the supply chain, ensuring that it can adapt to changes and challenges swiftly and effectively.
By collaborating effectively, organizations can navigate various challenges like demand volatility, supply chain disruptions and market uncertainties.
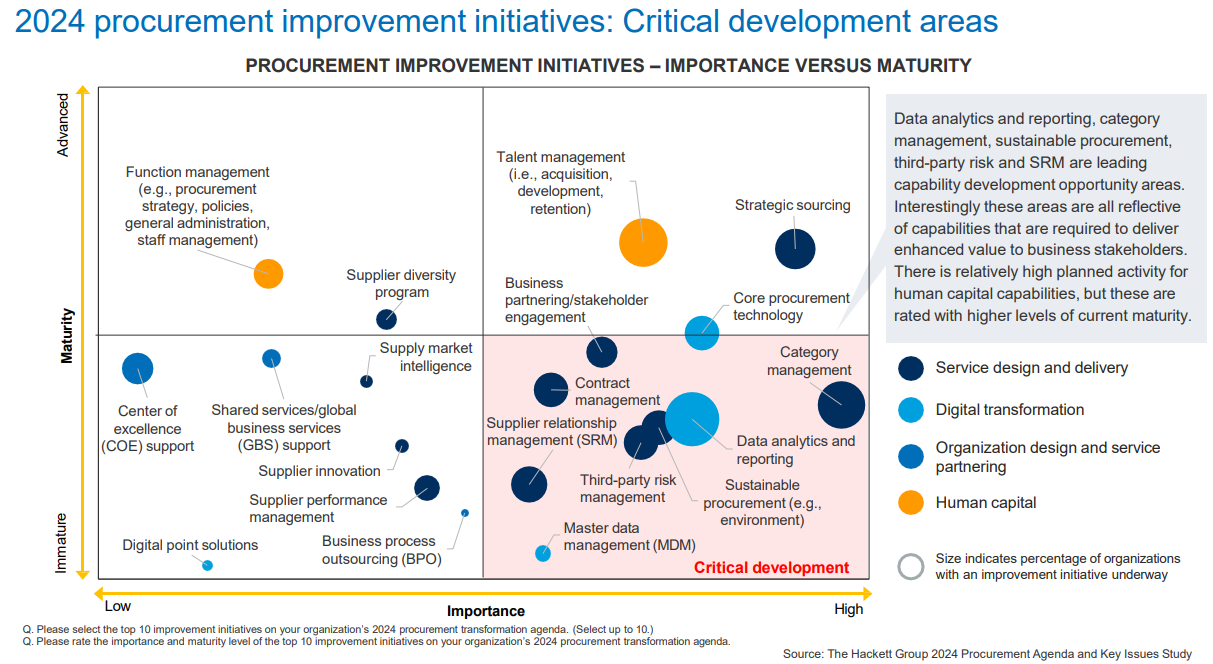
Types of Supply Chain Collaboration
There are several types of collaboration prevalent in supply chain management, each serving distinct purposes and involving different stakeholders.
- Horizontal collaboration: Cooperation among entities operating at the same level in the supply chain, such as contract manufacturers or retailers, to achieve shared objectives like cost reduction or market expansion.
- Vertical collaboration: Partner collaboration between entities at different levels of the supply chain, such as suppliers and manufacturers or manufacturers and distributors, to streamline processes, improve transparency and optimize value delivery.
- Cross-functional collaboration: Collaboration across different functional areas within an organization, such as procurement, production, logistics and marketing, to align activities, synchronize efforts and achieve overarching supply chain goals.
Every facet of collaboration plays a pivotal role in augmenting the overall performance and resilience of the supply chain. This collective endeavor not only strengthens operational capacities but also fosters a culture of innovation and continuous improvement, ensuring that the supply chain can adapt and thrive even in the face of unforeseen challenges.
Why is Supply Chain Collaboration Important?
Collaboration plays a crucial role in driving efficiency and reducing costs. By fostering strong partnerships and information sharing among stakeholders, organizations can streamline processes and eliminate redundancies to optimize resource allocation.
For instance, collaborative forecasting and long-term planning enables suppliers, manufacturers and distributors to synchronize their production schedules and inventory levels. This collaborative approach helps to minimize inventory holding costs and improve overall supply chain responsiveness. Collaborative forecasting and demand planning help to prevent overstocking or stockouts, reducing the risk of excess inventory or lost sales.
In another example focused on the ordering and fulfillment process, many manufacturers use planned orders that may include numerous releases of goods or materials on a scheduled cadence. These plans are critical to the production of goods, and through the addition of digital collaboration, changes can be streamlined, ensuring that production objectives are met, while also making the process of documenting and tracking changes to orders visible and simple for the procurement organization.
Inventory Collaboration and Vendor Managed Inventory are also key opportunities. At their core, these processes optimize working capital by providing visibility into stock and providing digital automation tools to manage the re-ordering of goods and materials.
Collaboration also supports cost-sharing initiatives, such as joint transportation or warehousing arrangements, allowing partners to leverage economies of scale and achieve cost efficiencies. It promotes innovation and knowledge exchange to support continuous improvement and the ability to adapt to changing market dynamics.
Challenges of a Supply Chain Collaboration
When global supply chains are fragmented and operating on different systems and key performance indicators (KPIs), problems can arise. One significant challenge is the lack of visibility and transparency across the supply chain network.
When each entity within the supply chain operates on disparate systems with varying data formats and protocols, it becomes difficult to obtain a holistic view of inventory levels, production schedules and transportation status. As a result, stakeholders struggle to make informed decisions, leading to inefficiencies, delays and increased costs.
Another challenge is inefficiency that can stem from disjointed processes, lack of coordination, and difficulty in accessing and interpreting data across the supply chain. As a result, organizations slow decision-making, suboptimal resource allocation, and an increased risk of errors and discrepancies. Ultimately, this leads to higher operational costs, missed opportunities and diminished overall performance.
Organizations may also find it difficult to coordinate with supply chain partners. Misaligned KPIs and divergent goals can lead to conflicting priorities – for example, one partner may prioritize cost reduction while another focuses on maximizing service levels. Fragmented supply chains face challenges in risk management and compliance, as well as inconsistent processes and standards across systems increase the risk of compliance violations or quality control issues.
Effective risk management and strong supplier relationships play a pivotal role in ensuring supply chain resilience and continuity. Research from The Hackett Group shows that organizations that maintain strong supplier relationships and have robust risk management strategies face 20% fewer supply chain disruptions than those with less effective supplier connections.
Organizations with robust supply chain risk management strategies proactively identify, assess and mitigate potential risks across their supply chain network. This proactive approach enables organizations and their suppliers to collaborate, anticipate and respond to disruptions more effectively, thereby minimizing their impact on operations. For more supplemental reading on preventing supply chain disruptions.
Furthermore, cultivating strong supplier relationships fosters collaboration, trust and transparency between buyers and suppliers. This collaborative environment enables timely communication, information sharing and joint problem-solving, which are essential for addressing challenges and mitigating risks. And, suppliers who perceive themselves as strategic partners are more likely to prioritize the buyer’s interests and proactively address issues that could potentially disrupt the supply chain.
Shared Visibility and Real-time Data in Supply Chains
Shared visibility and real-time data are indispensable components of effective supply chain collaboration. When all stakeholders have access to the same information in real time, they can make informed decisions promptly. This enables quicker responses to changes in demand, supply disruptions or other unforeseen events, improving overall agility and responsiveness across the supply chain.
By providing a common supply chain collaboration platform for communication and information sharing, shared visibility and real-time data help all parties closely align their activities, goals and objectives, supporting order scheduling, inventory management and, ultimately, reducing lead times. In the long run, this enhances customer satisfaction and brand loyalty.
Findings from The Hackett Group’s 2024 Procurement Agenda and Key Issues study emphasizes the need for greater agility and flexibility within procurement operations for adapting to changing market conditions, customer demands and regulatory requirements. Another crucial aspect is the drive towards digital transformation and the adoption of advanced technologies such as AI, machine learning and robotic process automation.
The study highlights the significance of supplier relationship management and collaboration, as well, emphasizing the need for closer alignment and collaboration to drive innovation, mitigate risks, and optimize supply chain performance. Furthermore, the report identifies sustainability and responsible sourcing as emerging priorities for procurement organizations.
How Can Supply Chain Collaboration Software Help?
Modern organizations can implement supply chain collaboration software to drive efficient and effective collaboration among all parties in the supply chain. By facilitating real-time communication and information sharing, these solutions enhance agility and flexibility within procurement teams, enabling them to easily navigate and quickly respond to changing market dynamics.
Leveraging advanced technologies such as AI and machine learning, more sophisticated supply chain collaboration solutions help organizations digitally transform, automating processes and gaining access to data for analysis and insights. Collaboration software also strengthens supplier relationships by fostering transparent communication and collaboration on joint initiatives, leading to improved performance and outcomes.
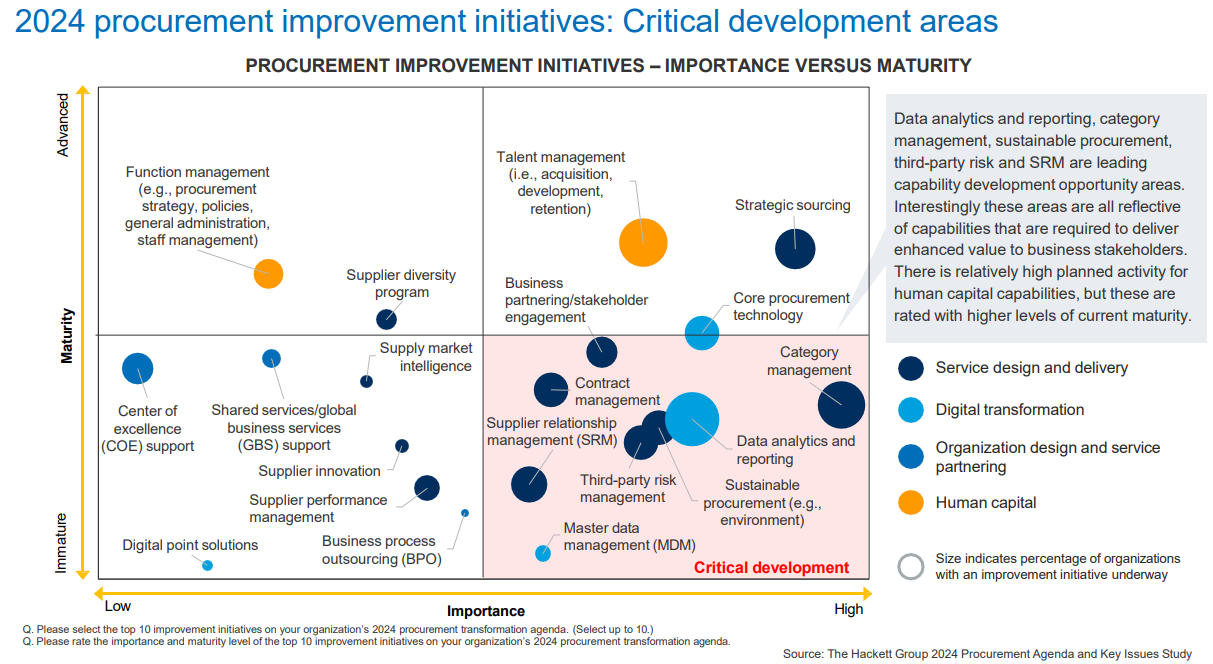
The Open Supply Chain Collaboration Model
The open supply chain collaboration model is based on three core pillars that collectively enhance supply chain efficiency and innovation.
- Knowledge exploration and exploitation, recognizing the value of leveraging both internal expertise and external insights to drive continuous improvement and innovation. This approach encourages organizations to actively seek new ideas, technologies and best practices while also capitalizing on existing knowledge assets.
- Horizontal and vertical collaboration, fostering partnerships not only across different departments within an organization but also with external stakeholders such as suppliers, distributors and customers.
- Incremental and radical innovation, recognizing that sustained success often requires a balance between making small, iterative improvements and pursuing more transformative changes. This flexibility allows organizations to adapt to evolving market dynamics, customer demands and technological advancements, ultimately driving long-term competitiveness and resilience.
By breaking down silos and facilitating seamless communication and cooperation, this collaborative framework enables smoother information flow and more integrated decision-making processes throughout the supply chain.
Let’s examine different ways collaboration supports suppliers, as well as manufacturing and distribution processes.
Supplier Collaboration
Collaborative efforts with suppliers play a pivotal role in enhancing sourcing, procurement and supplier relationship management (SRM). By engaging in open communication, sharing insights and aligning goals, organizations can leverage the expertise and resources of their suppliers to drive mutual value and achieve common objectives.
In sourcing, collaboration enables organizations to tap into supplier innovation, identify cost-saving opportunities and access new markets or technologies. The benefits of supplier network collaboration include streamlined processes, optimized inventory management and improved supply chain visibility. Fostering strong relationships with suppliers builds trust, transparency and accountability, leading to better performance, reduced risk and enhanced supplier loyalty.
Manufacturing Collaboration
Collaborative initiatives within manufacturing operations are essential for optimizing production processes and increasing efficiency. With strong teamwork and communication among various departments and stakeholders, organizations can identify bottlenecks, streamline workflows and implement best practices to enhance productivity.
One collaborative approach involves cross-functional teams comprising individuals from different departments and working together to solve complex problems and improve process efficiency. Additionally, leveraging advanced technologies like Internet of Things (IoT), AI and data analytics enables real-time monitoring of equipment performance and predictive maintenance.
Partnering with suppliers and service providers to implement lean manufacturing principles can lead to cost reductions, as well, resulting in shorter lead times and improved product quality.
Distribution and Partner Collaboration
Collaborative efforts with distributors and logistics partners play a crucial role in improving inventory management, transportation and order fulfillment. By working closely with these partners, organizations can achieve better visibility into inventory levels, demand fluctuations and supply chain performance.
Collaborative forecasting and demand planning initiatives allow for more accurate inventory replenishment and reduce stockouts, while coordination on transportation routes and schedules can optimize delivery times and reduce transportation costs and impact. Collaboration also helps accelerate order fulfillment and processing, enhancing customer satisfaction and loyalty.
Technology solutions such as electronic data interchange (EDI), transportation management systems (TMS), and warehouse management systems (WMS) enable the seamless exchange of between partners.
The Magic of Supplier Portals
Supply chain collaboration can be facilitated through procurement software and supplier portals to enhance efficiency, transparency and strategic alignment between partners. Here’s how:
- Transaction Integration: Procurement software and supplier portals enable simplify purchase orders, invoicing and payments between buyers and suppliers. This integration not only streamlines procurement processes but also reduces manual errors and accelerates payment cycles.
- Supply Chain Management Information Sharing: The EDI capabilities of supply chain software enable efficient exchange of critical supply chain information between trading partners, including data related to inventory levels, production forecasts and available capacity, bills of material (BOM) and other relevant supply chain data elements and metrics. With the ability to share data, organizations can optimize the production ordering process and inventory management.
- Strategic Collaboration: Supply chain management software and supplier portals also facilitate strategic collaboration initiatives aimed at enhancing supply chain resilience and strengthening supplier relationships. Through these platforms, organizations can engage in joint risk management efforts, supplier development programs and strategic sourcing initiatives to mitigate supply chain disruptions, drive innovation and achieve mutual business objectives.
Strategies for Successful Supply Chain Collaboration
Embracing digital technologies is a crucial aspect of this collaboration framework, as it enables seamless communication, real-time data sharing and process automation.
An Accenture survey revealed that companies implementing digital technologies in their supply chains, including advanced analytics and automation, experience a 30% boost in supply chain efficiency and a 35% decrease in operational costs. What’s more, adopting a supply chain collaboration framework supported by digital technologies can unlock new levels of efficiency, resilience and innovation.
Successfully fostering supply chain collaboration requires a multifaceted approach that addresses technological, organizational, and cultural aspects. One strategy is to invest in technology solutions that support collaboration, such as Unified Procurement Platforms. These platforms facilitate seamless data sharing across departments and enable real-time collaboration on sourcing, procurement and payment processes.
Another crucial aspect is process alignment, where organizations ensure that workflows are designed to support collaboration across Source-to-Pay (S2P) and Procure-to-Pay (P2P) processes. This alignment streamlines communication and decision-making, enhancing overall efficiency.
Additionally, encouraging a mindset shift towards collaboration is essential. Organizations must encourage a culture where collaboration with suppliers is valued and actively promoted. Finally, stakeholder engagement plays a pivotal role in fostering collaboration.
The graph below, from Ivalua’s New Procurement Playbook, illustrates the approaches considered most effective in building transparency and collaborative relationships within global supply chains. The data highlights several key strategies adopted by organizations to foster stronger partnerships with their suppliers.
At the forefront, 50% of respondents are prioritizing sharing more information with suppliers, signaling a shift towards greater transparency and trust, which enhances collaboration. Almost half (49%) stress the need for transparent and mutually beneficial contract negotiations, establishing stronger, value-driven partnerships. Another 40% focus on rationalizing the supplier base to facilitate better monitoring and deeper engagement.
Additionally, 31% are implementing technology to improve collaboration efficiency, recognizing the pivotal role of digital tools in streamlining communication and processes. Lastly, 30% are working with suppliers to mutually define objectives and improvement plans, ensuring alignment and continuous improvement in their partnerships.
Chassis Brakes: Successful Transformation Across Global Procurement and Supply Chain
Chassis Brakes International, a leading producer of disc brakes, drum brakes, electro-mechanical parking brakes and rotors for passenger cars and light commercial vehicles, embarked on a transformation journey to enhance its global procurement and supply chain operations.
The company aimed to streamline supplier management, rationalize its supplier base, centralize supplier master data and improve visibility into contracts and purchase order (PO) coverage. Some of the challenges they came up against included corrupt supplier master data, a large supplier base across multiple SAP ERP instances, poor visibility into indirect spend and regionally driven procurement processes.
By partnering with Ivalua, Chassis Brakes was able to reduce its supplier base by over 50% and enhance communication and collaboration with suppliers. They now have standardized PR/PO processes and centralized contract management. A seamless integration with SAP provides greater efficiency, and they’ve gained complete procurement contract visibility.
Ivalua has enabled our transformation journey effectively, making Procurement more agile and digital. It really began with a focus on suppliers and clean supplier master data to make better decisions. Resolving this empowered efficiency, visibility and much more value creation for the business.
Cyrille Naux, Vice President of Strategy, Operations and Procurement, Chassis Brakes International
Read the full Chassis Brakes International case study.
Solutions For Supply Chain Collaboration Software
Ivalua’s supply chain collaboration software offers a comprehensive suite of features designed to enhance collaboration and drive greater efficiency and agility across the supply chain. Some key features of Ivaula’s platform include:
- Real-time data sharing (unified data model): Real-time data provides immediate access to inventory levels, demand forecasts, production schedules and transportation updates, enabling all parties to make informed decisions and identify potential bottlenecks.
- Enhanced supply chain visibility: Early visibility into potential issues helps mitigate disruptions, enabling teams to proactively address risks and maintain operational flexibility to respond quickly to changes in demand or market conditions. This ensures continuity and efficiency, despite unplanned disruptions.
- Collaboration and forecasting features: By collaborating with suppliers on forecasting, organizations can gain insights into changes in supplier capacity, allowing them to adjust their plans accordingly and optimize their supply chain operations.
- Supplier portal: Centralizing and streamlining of supplier interactions within a unified portal simplifies order changes and confirmations, reducing manual efforts and minimizing errors. It helps to automate repetitive tasks and accelerate order processing times, as well.
- Analytics and reporting: Ivalua’s analytics and reporting tools enable organizations to identify trends, make data-driven decisions and generate customizable reports and dashboards. Through real-time visibility into critical metrics such as spend analysis, supplier performance and contract compliance, stakeholders can optimize supply chain processes and drive strategic initiatives for improved efficiency and effectiveness.
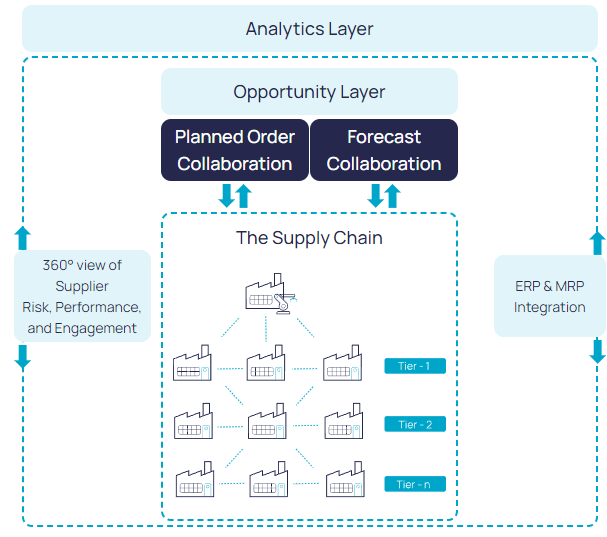
Conclusion
Effective supply chain collaboration is critical for modern businesses aiming to optimize efficiency, reduce costs, and enhance overall performance. By fostering transparent communication, leveraging digital technologies, and aligning goals with suppliers, companies can build resilient and responsive supply chains.
This collaborative approach not only mitigates risks but also drives innovation, ensuring that organizations can adapt swiftly to market changes and customer demands and secure a competitive edge in the dynamic global marketplace.
Start investing in your supply chain by watching Ivalua’s supply chain collaboration software demo, and unlock new levels of agility, visibility, and performance across your supply chain networks.